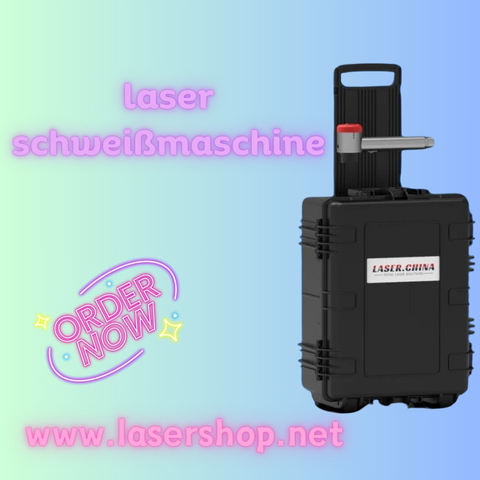
Metalle wie Kupfer, Aluminium oder Messing sind in der industriellen Fertigung alltäglich geworden – besonders im Bereich Elektrotechnik, Automobilbau und Luftfahrt. Diese Materialien sind für ihre hohe Wärmeleitfähigkeit und Reflexion bekannt, was bei klassischen Schweißverfahren erhebliche Herausforderungen darstellt. Doch mit dem technologischen Fortschritt und der zunehmenden Verbreitung von Laser Schweißmaschinen hat sich die Bearbeitung solcher Werkstoffe revolutioniert. Aber: Nicht jede Laser Schweißmaschine ist für hochreflektierende Metalle geeignet. Was also sind die konkreten Anzeichen, die darauf hindeuten, dass ein Gerät dafür geschaffen ist?
Die Physik hinter reflektierenden Materialien
Bevor man sich mit der Laser Schweißmaschine beschäftigt, lohnt sich ein kurzer Blick auf die physikalischen Eigenschaften der Metalle selbst. Kupfer beispielsweise hat einen Reflexionsgrad von über 95 % bei Wellenlängen im Infrarotbereich – genau dort, wo viele Laser arbeiten. Das bedeutet: Ein Großteil der Energie wird nicht absorbiert, sondern reflektiert. Das hat zwei Folgen: Die Energie reicht nicht aus, um die Oberfläche effektiv zu schmelzen, und zweitens besteht die Gefahr, dass der reflektierte Laserstrahl optische Komponenten beschädigt.
Eine geeignete Laser Schweißmaschine muss diese Herausforderungen meistern – nicht durch rohe Leistung, sondern durch technische Präzision und abgestimmte Prozesse.
Wellenlänge und Absorption: Der entscheidende Unterschied
Ein kritischer Indikator für die Eignung einer Laser Schweißmaschine ist die Wellenlänge des verwendeten Lasers. Während CO₂-Laser bei 10.600 nm arbeiten, setzen moderne Geräte auf Faserlaser mit 1.064 nm. Faserlaser bieten eine bessere Fokussierbarkeit, aber auch sie stoßen bei Kupfer an Grenzen.
Neuentwicklungen gehen deshalb in Richtung Ultrakurzpuls-Laser oder Laserquellen mit angepasster Wellenlänge, z. B. grüne Laser bei 515 nm. Diese haben eine deutlich höhere Absorptionsrate bei Kupfer und Aluminium und eignen sich daher für kritische Anwendungen.
Eine Laser Schweißmaschine, die solche Quellen verwendet, zeigt deutlich, dass sie für hochreflektierende Metalle ausgelegt ist.
Strahlqualität und Fokusdurchmesser
Die Eignung zeigt sich auch an der Strahlqualität. Eine hohe Strahlqualität (gemessen im sogenannten M²-Wert) ermöglicht es, den Laserstrahl auf einen kleineren Punkt zu fokussieren, was die Leistungsdichte erhöht. Bei hochreflektierenden Metallen ist dies entscheidend, da ein kleinerer Fokuspunkt eine höhere lokale Temperatur bedeutet, was wiederum die Schmelzbildung erleichtert.
Eine professionelle Laser Schweißmaschine wird oft mit einer adaptiven Optik ausgestattet, die den Fokusdurchmesser dynamisch anpassen kann – ein weiteres Indiz für Eignung bei schwierigen Materialien.
Pulsleistung vs. Dauerleistung
Ein weiteres technisches Kriterium ist die Leistungsabgabe. Kontinuierliche Laser können schnell zu Wärmestaus führen, besonders bei Materialien mit hoher Wärmeleitfähigkeit wie Aluminium. Pulsierende Laser hingegen geben Energie in kurzen, intensiven Impulsen ab, die es ermöglichen, die Oberfläche zu schmelzen, ohne dass zu viel Wärme in das Bauteil eindringt.
Werden beim Modell kurze Pulsdauern (im Mikro- oder Nanosekundenbereich) genannt, ist das ein deutliches Zeichen dafür, dass die Laser Schweißmaschine auf kritische Materialien ausgelegt ist.
Prozessüberwachung und Rückkopplungssysteme
Moderne Laser Schweißmaschinen für reflektierende Metalle verfügen über integrierte Rückmeldesysteme. Sie messen in Echtzeit Parameter wie Temperatur, Reflexionsgrad oder Einschweißtiefe und justieren den Prozess automatisch. Dies ist nicht nur eine Frage der Qualitätssicherung, sondern entscheidend für den Materialschutz.
Ohne solche Systeme riskiert man nicht nur defekte Werkstücke, sondern auch den Ausfall optischer Komponenten durch Rückreflexion – ein nicht zu unterschätzendes Problem bei Kupfer.
Praktischer Einsatz: Ein Blick in die Fertigung
In der Praxis zeigen sich geeignete Laser Schweißmaschinen besonders im Bereich der Batteriefertigung für Elektrofahrzeuge. Dort werden Kupfer- und Aluminiumverbindungen unter extrem engen Toleranzen geschweißt – häufig automatisiert, in Reinräumen, mit hoher Wiederholgenauigkeit.
Hier kommen überwiegend grüne Faserlaser oder Lasersysteme mit spezieller Pulskontrolle zum Einsatz. Der Schweißprozess wird über Kamera- und Sensoriksysteme überwacht, jede Naht dokumentiert und analysiert. Eine gewöhnliche Laser Schweißmaschine, wie sie in der Metallverarbeitung zum Einsatz kommt, wäre mit diesen Anforderungen überfordert.
Wartung und Kalibrierung – ein kritisches Thema
Gerade bei der Bearbeitung reflektierender Materialien ist es wichtig, dass die Optik und Laserquelle in optimalem Zustand sind. Schon kleinste Verunreinigungen oder Abweichungen in der Strahlführung können dazu führen, dass der Schweißprozess fehlschlägt.
Professionelle Systeme bieten daher automatische Kalibrierungsprozesse, Luftfiltersysteme zur Staubvermeidung und geschlossene Kabinen zur Prozesssicherheit. Auch dies spricht für eine spezifische Ausrichtung der Laser Schweißmaschine.
Sicherheitsmaßnahmen gegen Rückstrahlung
Ein ganz praktischer Punkt: Jede Maschine, die für reflektierende Metalle gebaut wurde, verfügt über spezielle Sicherheitseinrichtungen gegen rückreflektierten Laserstrahl. Diese Sicherheitsmechanismen verhindern, dass zurückgeworfene Strahlung in das Lasersystem eindringt oder den Bediener gefährdet.
Das können Schutzfenster mit spezieller Beschichtung sein, automatische Abschaltvorrichtungen oder reflektionsarme Innenverkleidungen. Wer eine solche Ausstattung vorfindet, kann davon ausgehen, dass die Laser Schweißmaschine für kritische Metalle entwickelt wurde.
Final Thoughts
Nicht jede Laser Schweißmaschine ist für hochreflektierende Metalle wie Kupfer oder Aluminium gemacht – auch wenn dies oft angenommen wird. Es braucht mehr als nur Leistung, um diese Materialien sicher und präzise zu verarbeiten. Wellenlänge, Pulstechnik, adaptive Fokussierung, Prozessüberwachung und Sicherheitsmaßnahmen sind klare Anzeichen dafür, ob ein System wirklich dafür ausgelegt ist. Wer regelmäßig mit solchen Materialien arbeitet, sollte sich daher nicht von allgemeinen Leistungsangaben täuschen lassen, sondern gezielt nach diesen technischen Eigenschaften Ausschau halten. So gelingt der Einstieg in die Hochpräzisionsbearbeitung – sicher, zuverlässig und wirtschaftlich.