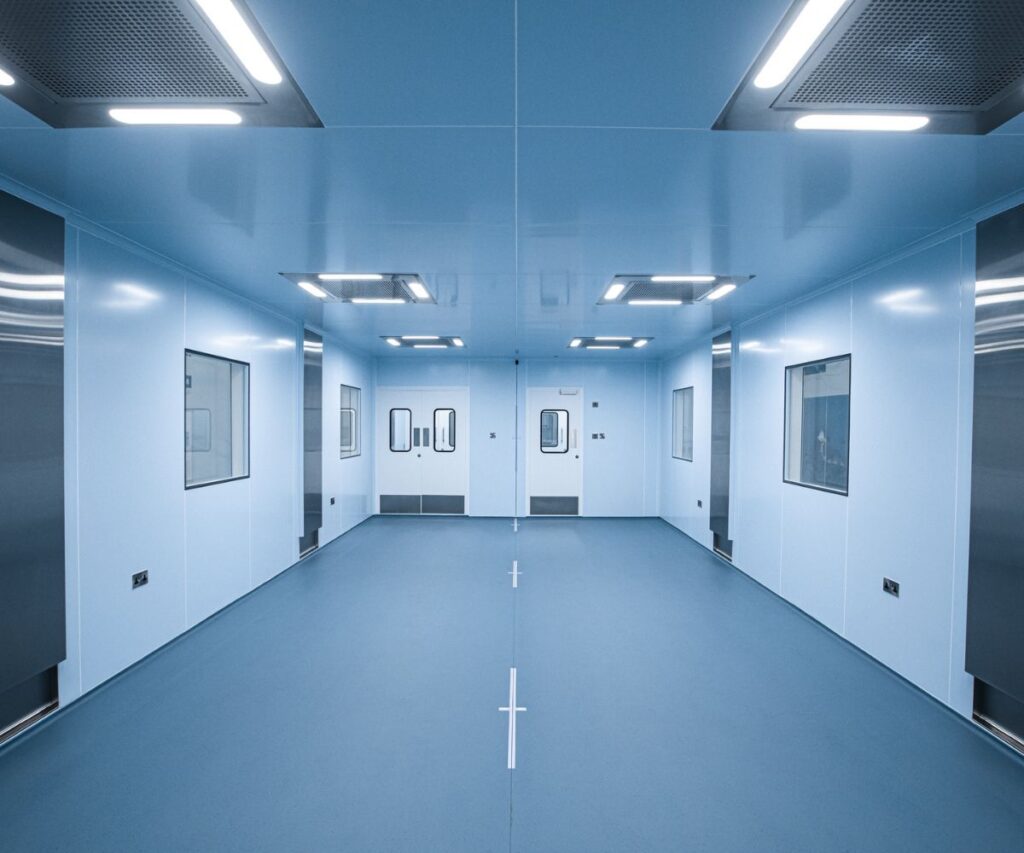
Introduction to Prefabricated Clean Rooms in Singapore’s Pharmaceutical Sector
In Singapore’s evolving pharmaceutical industry, the demand for prefabricated clean rooms has seen a substantial rise. These controlled environments are critical for ensuring GMP (Good Manufacturing Practice) compliance, contamination control, and product quality assurance. As an international hub for biopharmaceutical manufacturing, Singapore leverages prefabricated clean room systems to meet stringent regulatory requirements while maintaining agility and scalability in operations.
What is a Prefabricated Clean Room?
A prefabricated clean room is a modular, factory-fabricated, and quick-to-install environment designed to maintain controlled levels of airborne particles, temperature, humidity, and pressure. These rooms are constructed using modular panels, HEPA/ULPA filters, and advanced HVAC systems to meet ISO standards and clean room classifications. Prefabricated clean rooms are favour for their shorter construction time, cost-effectiveness, and flexibility compare to traditional build-outs.
Role of Prefabricated Clean Rooms in Pharmaceutical Manufacturing
1. Contamination Control and Sterility
In pharmaceutical manufacturing, maintaining sterile production environments is non-negotiable. Prefabricated clean rooms in Singapore are engineered to prevent contamination from airborne microbes, particles, and other pollutants. They enable the manufacturing of sterile injectables, biologics, and active pharmaceutical ingredients (APIs) under rigorously monitored conditions.
- Airlocks, pass-through chambers, and interlocked doors maintain pressure differentials.
- The use of HEPA filters (High-Efficiency Particulate Air) ensures a particle-free air supply.
- Controlled entry and exit procedures further mitigate cross-contamination risks.
2. Compliance with International Standards
Singapore’s pharmaceutical industry aligns with WHO GMP, US FDA, and EU GMP standards. Prefabricated clean rooms help manufacturers meet these regulations with ease due to the following:
- Modular components are pre-certified for clean room use.
- Validated HVAC and filtration systems for consistent performance.
- Easy documentation of environmental controls and SOP integration.
These rooms are often classified under ISO 5 to ISO 8, depending on the pharmaceutical product’s requirement.
3. Flexibility and Scalability
Pharmaceutical companies in Singapore benefit from the modularity of prefabricated clean rooms. They can be expand, relocated, or reconfigured as production demands change, offering unmatched operational flexibility.
- Suitable for pilot plants, R&D facilities, and full-scale production.
- Quick upgrades to meet new drug pipeline requirements.
- Adaptability to various pharmaceutical processes like sterile compounding, packaging, and quality testing.
Key Components of Prefabricated Clean Rooms in Singapore
Modular Wall and Ceiling Panels
These are constructed using non-shedding materials like powder-coated steel, aluminium honeycomb cores, and antimicrobial finishes to prevent microbial growth and particle accumulation.
HVAC and Air Filtration System
An advanced HVAC system maintains air change rates, temperature, and relative humidity, while HEPA or ULPA filters ensure particle filtration down to 0.3 microns or less.
Lighting and Electrical Integration
LED lighting systems are flush-mounted to reduce particle collection. Electrical controls, intercoms, and BMS (Building Management Systems) are seamlessly integrated.
Clean Room Flooring
Anti-static, seamless vinyl or epoxy flooring is use to withstand chemical cleaning, resist bacterial growth, and support heavy pharmaceutical equipment.
Air Showers and Gowning Rooms
To support personnel hygiene, air showers and gowning rooms reduce external contamination and maintain internal cleanliness integrity.
Benefits of Prefabricated Clean Rooms for Singapore’s Pharmaceutical Industry
Reduced Time-to-Operation
Traditional clean room construction can take several months, whereas prefabricated clean rooms can be deployed in a fraction of the time, reducing the time to start production and increasing speed to market.
Lower Capital Investment
With less on-site labor and shorter construction timelines, pharmaceutical companies enjoy significant cost savings, making CAPEX planning more efficient.
Simplified Maintenance
Prefabricated clean rooms in Singapore are design for easy access, quick filter replacements, and systematic maintenance schedules. This ensures minimal downtime and extended equipment life.
Energy Efficiency
Integrated energy-saving systems such as smart HVAC, low-energy lighting, and automated controls reduce operational costs while maintaining regulatory compliance.
Clean Room Classifications in the Pharmaceutical Industry
In Singapore, pharmaceutical clean rooms adhere to ISO and GMP classifications:
- ISO 5 (Class 100): For aseptic filling, sterile compounding, and critical operations.
- ISO 6-7 (Class 1,000 – 10,000): Used in formulation, weighing, and coating processes.
- ISO 8 (Class 100,000): For non-sterile production and support areas.
These classifications define allowable particle counts, pressure differentials, and air change rates essential for product safety and regulatory adherence.
Applications of Prefabricated Clean Rooms in Singapore’s Pharmaceutical Facilities
Biologics and Vaccine Production
Singapore is a key player in global biologics manufacturing. Prefabricated clean rooms provide the required aseptic environment for the production of monoclonal antibodies, cell therapies, and vaccines.
Sterile Fill-Finish Operations
For injectable drug products, sterility assurance is crucial. Clean rooms facilitate aseptic filling, vial sealing, and final packaging under stringent conditions.
Quality Control and Microbiology Labs
Labs require low particulate zones for sterility testing, microbial limit testing, and chemical assays. Prefabricated solutions provide compliant and validated spaces for laboratory functions.
Research and Development (R&D)
R&D facilities need versatile environments for multiple formulations and trials. Modular clean rooms support adaptable layouts for changing protocols and equipment.
Why Singapore Prefers Prefabricated Solutions
Singapore’s focus on biomedical excellence is driven by:
- Government support for pharma infrastructure development.
- A growing number of contract development and manufacturing organizations (CDMOs).
- Increasing foreign investment in pharmaceutical plants.
Prefabricated clean rooms align with this vision by enabling fast-track construction, regulatory compliance, and sustainable growth in a high-stakes industry.
Read Also: Wear Your Own Style with a Spider Hoodie
Conclusion
In Singapore’s pharmaceutical landscape, prefabricated clean rooms serve as the backbone of GMP-compliant manufacturing. Their integration of cutting-edge technology, modular design, and regulatory alignment ensures that pharmaceutical companies can innovate swiftly, manufacture safely, and compete globally. As the demand for precision and compliance grows, these clean rooms will continue to play a pivotal role in pharmaceutical excellence in Singapore and beyond.