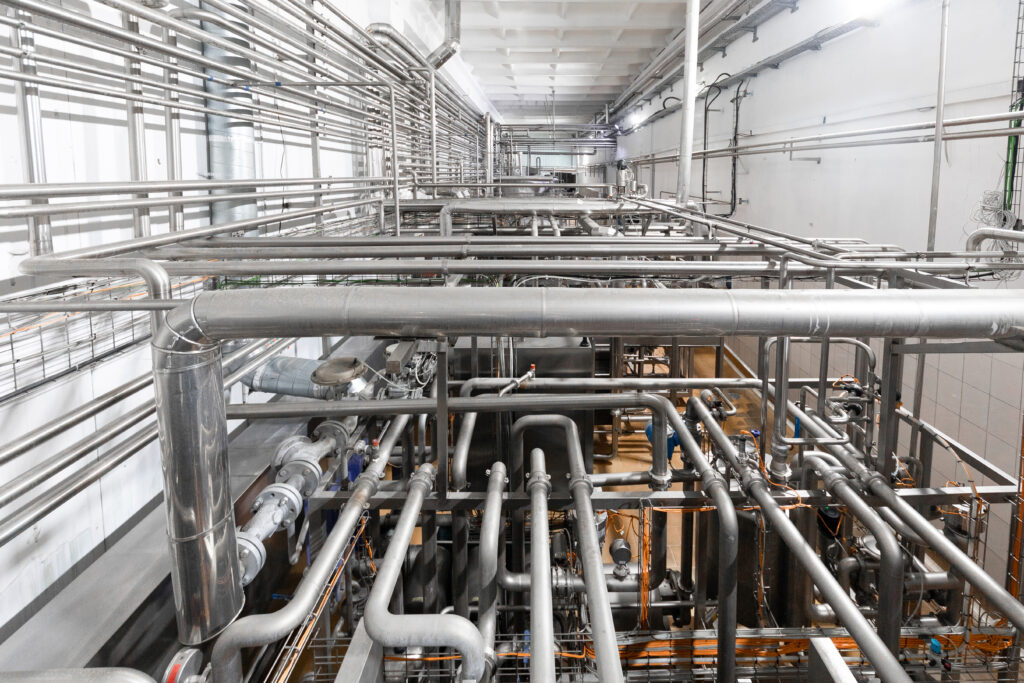
chill water piping
Chilled water piping is a key part of many cooling systems. It moves chilled water from a central chiller to different parts of a building. This system helps control the temperature in homes, offices, factories, and other spaces.
But over time, chill water piping can develop problems. These issues can affect performance, increase running costs, and even damage the building. Let’s look at the common problems in chill water piping and how to fix them.
What Is Chill Water Piping?
Chill water piping carries cold water to air handlers or fan coil units. These units use the cold water to cool the air before sending it into rooms. The water then returns to the chiller to be cooled again. This cycle keeps repeating. The pipes are usually insulated to keep the water cold and prevent moisture from forming outside the pipes.
Common Problems in Chill Water Piping Systems
Leaks and Water Damage
Leaks are common in older chilled water systems. Pipes can crack, joints can loosen, and valves can fail. Even a small leak can cause water loss, low pressure, and higher energy use. Leaks also increase the risk of mould or damage to walls, ceilings, or floors.
Fix:
- Check for water stains, damp spots, or puddles.
- Repair small leaks with sealing materials.
- Replace broken valves, joints, or pipe sections.
- Keep pipe supports in place to prevent movement that may cause cracks.
Air in the Pipes
Air can enter the system through leaks or during maintenance. Trapped air forms bubbles that slow the water flow. This leads to uneven cooling and puts stress on the pumps.
Fix:
- Use manual or automatic air vents to release trapped air.
- Inspect areas with gurgling sounds or poor cooling.
- Make sure all pipe joints are tightly sealed.
Corrosion and Rust
Metal pipes, especially older ones, may rust over time. Poor water quality and incorrect pH levels speed up this process. Corrosion can cause blockages, leaks, and weak pipe walls.
Fix:
- Use pipes made from corrosion-resistant materials.
- Inspect pipes for rust marks or flakes.
- Maintain the correct water chemistry.
- Remove and replace badly corroded sections.
Poor Insulation
Chill water piping must be well insulated. Without proper insulation, cold pipes attract moisture from the air. This causes dripping water and energy loss. Over time, this can damage nearby equipment and building materials.
Fix:
- Inspect all insulation for cracks, gaps, or missing parts.
- Replace damaged insulation.
- Make sure fittings, valves, and bends are fully covered.
Blockages in the System
Sediment, dirt, or algae can build up inside the pipes. This reduces the water flow and leads to poor cooling. It also increases pressure on the pumps and uses more energy.
Fix:
- Flush the system to remove debris.
- Clean filters and strainers regularly.
- Check for slow water flow or changes in cooling.
Expansion and Contraction
When pipes get cold or warm, they expand and shrink. This natural movement puts stress on joints and pipe supports. If not handled well, it can lead to cracks, misalignment, or pipe failure.
Fix:
- Use flexible joints or loops to handle pipe movement.
- Allow space in supports for movement.
- Inspect joints for signs of stress or movement.
Vibration and Noise
Pumps and flowing water can cause vibrations in the piping. If the pipes are not fixed well, this leads to rattling sounds or pipe damage. Vibrations also increase wear on pipe joints.
Fix:
- Secure pipes with strong supports.
- Use vibration isolators at key points.
- Check for noise or shaking during system operation.
How to Prevent Problems
Prevention is better than repairs. Keeping your chill water piping in good shape saves money and avoids sudden failures.
Regular Inspection
Inspect the system at set intervals. Look for leaks, rust, loose joints, or signs of wear. Use a checklist to stay consistent.
Routine Cleaning
Flush the pipes to remove scale and dirt. Clean or replace filters and strainers. This keeps water flowing well and protects pumps.
Pressure Checks
Watch the system pressure. Both high and low pressure cause trouble. Use gauges to track any pressure changes. Fix leaks or clogs as needed.
Water Quality
Keep the water clean. Use proper water treatment to control pH and reduce minerals that cause rust or scale. Dirty water leads to build-up and damage.
Maintain Insulation
Repair or replace worn insulation. Moisture around pipes is a sign the insulation has failed. Good insulation saves energy and avoids water damage.
Secure Pipe Supports
Loose pipes move more and are at risk of breaking. Check brackets, hangers, and supports. Make sure they hold the pipes firmly but allow movement when needed.
Signs Your System Needs Attention
It helps to know the early warning signs. Catching problems early makes them easier to fix.
Uneven Cooling
If some rooms are warm while others are cold, the problem may be in the chilled water piping. It could be air, a blockage, or poor flow.
Higher Energy Bills
When the system works harder due to leaks or clogs, it uses more energy. A sudden rise in energy use often points to an issue.
Strange Noises
Rattling, hissing, or banging noises mean something is wrong. It may be air in the pipes, loose supports, or pump strain.
Water Stains or Damp Areas
Moisture on walls or ceilings near the pipes may come from a leak. Stains or mould are strong signs to inspect the area.
Upgrading Old Systems
If your system is more than 20 years old, it may be time to plan for an upgrade. Older chill water piping may be less efficient and more likely to fail.
Why Upgrade?
- New materials resist rust better.
- Improved insulation reduces energy loss.
- Smart designs reduce wear and allow easy maintenance.
Planning the Upgrade
- Inspect all pipes and list areas with recurring problems.
- Choose materials like copper or high-grade plastic.
- Make sure the system has space for expansion and access for repairs.
Step-by-Step Approach
- Start with the most damaged sections.
- Upgrade in phases to manage cost.
- Test the system after each phase to spot problems early.
Conclusion
Chill water piping systems are vital for cooling in many buildings. But they need proper care to stay reliable. Common issues like leaks, rust, blockages, or poor insulation can hurt system performance. These problems also raise energy costs and can cause damage to the building.
Fixing these problems often involves simple steps like replacing worn parts, cleaning pipes, or sealing joints. But the best way to keep the system in good shape is through regular checks and maintenance.
Watch for signs like uneven cooling, strange noises, or water stains. Respond early to keep your chill water piping working well. And if your system is getting old, think about upgrading parts of it. Taking care of your chill water piping is not just about comfort. It helps you save money, avoid damage, and keep your building running smoothly.