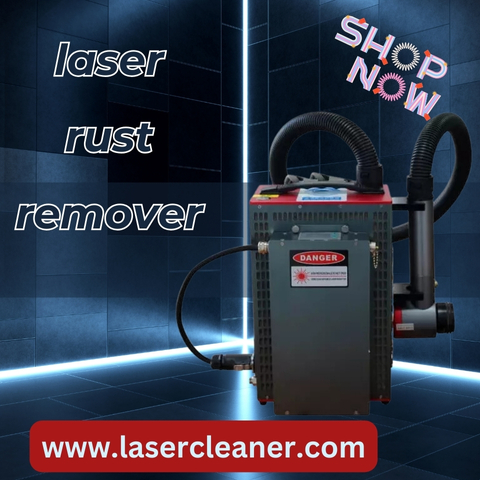
The rusting of metal is not just a cosmetic issue—it weakens structures, ruins machinery, and drives up maintenance costs. Traditional rust removal methods often bring new problems: abrasive damage, chemical residue, or even loss of metal thickness. But what if there’s a method that removes rust without any mechanical contact, grinding, or harsh chemicals? This is where a laser rust remover enters the scene—an innovation that’s reshaping how industries handle corrosion.
But the question remains: can a laser rust remover clean metal without damaging its structural integrity or composition? To answer that, we need to dive deep into how this tool works, how metal surfaces react to laser energy, and what real-world usage tells us.
The Science Behind Laser Rust Removal
At its core, a laser rust remover uses a focused beam of light to irradiate the rust layer. This laser beam is tuned to a specific wavelength and power level so that it interacts primarily with contaminants (like rust, oxides, or paint) while leaving the underlying base metal untouched. Rust, being a chemically different substance (typically iron oxide), absorbs laser energy differently than solid metal.
The laser energy heats and vaporizes the rust without physically touching the metal. When done correctly, the base material remains cool and unaffected. This principle is called laser ablation.
This process is highly controlled. Operators can adjust:
-
Power levels
-
Pulse duration
-
Frequency
-
Scanning speed
These variables are critical. The aim is to vaporize only the surface contaminants without generating enough heat to penetrate or affect the underlying metal structure.
Is There Heat? Yes. Is There Damage? No—If Done Right
Let’s be clear: lasers generate heat. That’s the nature of energy transfer. But what makes a laser rust remover safe for metal is the precision. Compared to a grinding disc or sandblaster, which exerts mechanical force across a wide area, laser cleaning is localized and controllable.
For example, in tests performed on stainless steel, aluminum, and mild steel:
-
A pulsed laser at 1000W removed oxidation and rust layers effectively.
-
Infrared thermography showed the temperature on the base metal remained below 150°C.
-
No warping, discoloration, or microcracking was detected.
The rust simply vaporized, leaving behind a clean, structurally sound surface.
This is why laser rust removers are used on:
-
Aerospace components
-
Automotive frames
-
Heritage restoration
-
Medical equipment
In all these cases, preserving the integrity of the metal is critical.
What About Surface Composition?
Some users worry that intense laser exposure might alter the composition of the base metal. This is a valid concern—especially for high-precision components in aerospace or medical fields.
However, laser rust removers operate on a surface level—microns deep. The laser beam doesn’t reach the bulk of the material, so the alloy’s internal properties remain unchanged.
Multiple spectroscopic studies confirm:
-
No changes in elemental composition post-cleaning.
-
No carbon migration, oxidation, or hardening beneath the cleaned area.
-
No introduction of foreign elements or residue.
In fact, because the method is non-contact, there’s no abrasive contamination (which is a common problem with sandblasting or grinding).
Cleaning Depth and Selectivity
Laser rust removers allow operators to control the cleaning depth with high precision. This means:
-
You can remove just the rust, leaving protective coatings beneath untouched.
-
You can selectively clean weld seams without stripping adjacent paint.
-
You can preserve sensitive textures or stamps on the surface.
This level of control is unmatched by traditional methods.
Industrial users often program robots or CNC arms to clean specific patterns, avoiding unnecessary exposure and preserving delicate surfaces. In shipyards and aircraft maintenance bays, this precision is essential—not just for safety, but for compliance with engineering tolerances.
Industrial Use Cases That Prove the Concept
Let’s look at some real-world examples.
1. Automotive Restoration
In classic car restoration, the use of a laser rust remover has become popular for removing rust from chassis, engine blocks, and wheel arches. A 1500W pulsed laser can clean rust without damaging VIN numbers, embossed logos, or delicate edges.
2. Power Plants
Nuclear and thermal power stations use laser rust removers to clean heat exchangers and steam piping without removing material or requiring shutdown. The cleaning process maintains the integrity of pressure-rated components, avoiding any structural compromise.
3. Aerospace Components
Aircraft engine components—especially turbine blades—are cleaned using laser technology. The structural integrity of titanium and nickel alloys must be preserved to avoid catastrophic failure. Laser systems, when calibrated, remove oxidation from surface cracks for inspection, without deep penetration.
4. Military and Defense
In weapons maintenance, such as tank barrels or aircraft carriers, removing rust without changing the barrel’s bore or compromising armor plating is essential. Here, laser cleaning is not just efficient—it’s trusted for preserving life-critical assets.
Are There Conditions Where Lasers May Damage Metal?
Yes—but only in improper use cases.
If:
-
Power levels are too high
-
The laser beam is held stationary on one spot too long
-
There’s no movement or pulse control
-
The operator is untrained
…then heat buildup can occur. This might cause:
-
Discoloration
-
Micro warping
-
Surface hardening
But these are operational errors—not inherent flaws in the technology. That’s why industrial laser rust removers come with pre-programmed settings, safety interlocks, and often computer guidance.
The Role of Training and Calibration
The effectiveness and safety of a laser rust remover depends heavily on:
-
Correct equipment selection (power, wavelength)
-
Material type (steel, aluminum, copper)
-
Operator training
-
Surface preparation
Certified operators or automated systems typically run tests on sample sections before full-scale cleaning. This ensures calibration is precise and avoids any unintended surface damage.
Is This Technology Expensive?
While the initial cost of a laser rust remover is higher than sandblasters or chemical baths, the total cost of ownership is lower. Why?
-
No need for abrasives, chemicals, or media refills
-
Minimal waste disposal
-
No surface rework or refinishing
-
Longer equipment life due to no mechanical contact
In the long term, industries save on labor, consumables, and downtime.
Final Thoughts
The idea that laser rust removal might damage metal is a common concern, but in reality, it’s based on outdated assumptions. A laser rust remover—when correctly used—is one of the most precise, non-invasive methods available for decontaminating and restoring metal surfaces. It doesn’t grind, scrape, or chemically alter the material. It simply uses controlled energy to vaporize rust, leaving the underlying structure untouched.
Whether you’re dealing with high-value aerospace parts, vintage automotive bodies, or sensitive manufacturing components, this technology offers a clean, safe, and repeatable way to maintain metal without risking structural integrity. As more industries adopt this approach, it’s becoming clear: the future of rust removal is contactless, chemical-free, and laser-sharp.