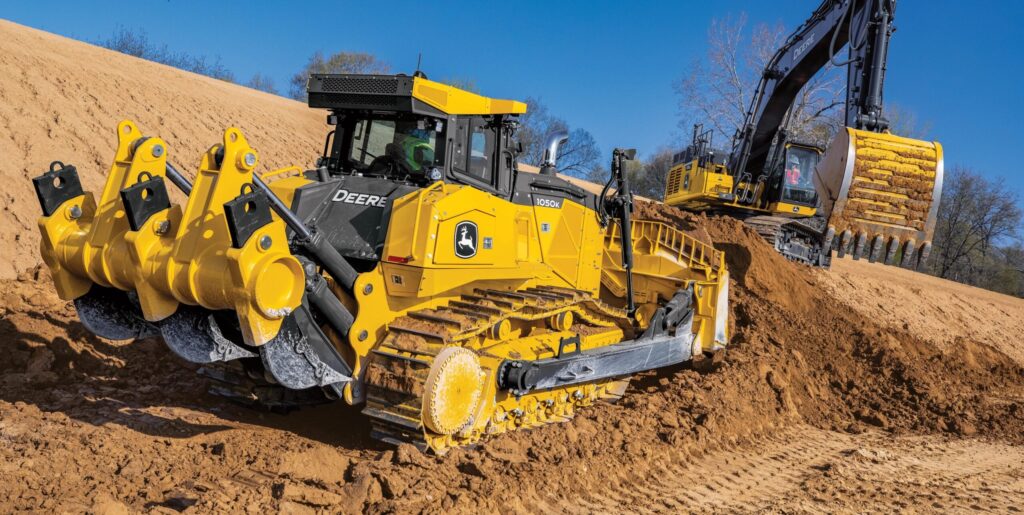
Earth-moving equipment is the lifeline of the construction, mining, and infrastructure industries worldwide. These leviathans of industry are not merely powerful machines, they are examples of cutting-edge engineering meant to alter the landscape itself. But underneath all that heavy machinery, there is a well-thought-out journey that goes from the concept to completion. The concept of understanding how earth movers are engineered creates a vast world of innovation, safety precautions, and mechanical genius that has powered the modern world. When it comes to the competitive industries today, the need for machines that could fulfill accurate requirements is higher than ever before, and engineering plays an important role in maintaining all the projects on time and on budget, and targeting the specific needs.
From Concept to Drafting Table
All earth-moving equipment starts as an idea, whether born from an industry demand or a performance challenge. Engineers, designers, and product developers collaborate to evaluate what is missing in the market or what improvements can enhance current models. CAD software plays a central role in the early phase, enabling teams to simulate movement, stress points, and structural behavior. In a virtual 3D space, these “digital prototypes” are the first step toward creating real machines capable of withstanding the demands of heavy-duty operations. This process involves multiple iterations and feedback loops across departments, ensuring every machine aligns with technical feasibility, user needs, and regulatory standards. Without this early stage of digital engineering, producing effective and affordable equipment would be far more costly and time-consuming.
Material Selection and Structural Strength
An earth mover’s bones are exposed to extreme stress, weight, and conditions. This makes the selection of materials a key phase in the engineering process. There are various alloys of steel that are widely used for the frame and arms; for other parts, aluminum alloys or composites are used for weight efficiency. Stress analysis tests are done by engineers to ensure that there is no unnecessary stress on the structural integrity. Strength, durability, and weight form the balance that determines whether a machine can work in challenging environments. Moreover, the corrosion resistance, as well as the weldability and fatigue life, are examined. The components have to work without errors under heavy load cycles and abusive modes of operation, frequently in remote areas where access for repair is not readily available. These machines are not only strong but also structurally strategic.
Powertrain and Hydraulics Integration
The raw muscle to push, dig, or lift is necessary but not sufficient for the completion of construction vehicles or earth movers. Engine choice is based on the power output, fuel efficiency, and compliance with emissions. But underneath the engine is a complex system of hydraulics. These systems are responsible for converting the power of an engine into mechanical force, moving arms, booms, and buckets. Hydraulic systems need to be carefully routed, sealed, and pressure-tested in order to prevent leaks and ensure responsive control. Even the whole powertrain from the diesel engine to the final drive is fine-tuned for reliability and output. Also, control systems are calibrated to provide an easy-to-use, user-friendly environment with minimal wear over time.
Operator Cabin Design and Safety Systems
Human comfort and safety are some of the factors in modern earth mover engineering. The operator cabin, which is frequently elevated high above the ground, is designed for visibility, ergonomics, and fatigue. Engineers integrate climate control, suspension seats, joystick controls, and digital displays that check the health of the machines. Rollover protection structure (ROPS), backup cameras, alarms, and reinforced glass are now commonplace in terms of safety systems. From a metal box, it has developed into a smart, safe command center. Some of the more recent developments include touch interface screens, haptic feedback, and real-time diagnostic alerts. These innovations go a long way in lowering human error while boosting productivity.
Testing and Prototyping
Earth movers must also undergo a rigorous series of tests before they hit the market. Full-scale prototypes are constructed and run through obstacle courses, simulated job sites, and harsh weather. These trials put the car through all kinds of maneuverability and load capacity, engine stress, and braking. Engineers collect data, meddle with components, and fine-tune the design until the equipment operates to specification. This stage guarantees that when it comes to the release of the final product, it can work safely and effectively under a wide range of job conditions. User trials that involve seasoned operators are also part of testing to get feedback on control layout, visibility, and comfort. Resulting in a product that is not just useful, but it is field-tested, or to say it is user-approved.
Final Phase
Mass production is the last stage in the engineering process. Designs get approved, and materials as well as components are produced at this stage. Robot assembly lines, highly qualified technicians, and quality control teams labor together to make earth movers come alive. Each machine is carefully constructed, checked, and tested before it is delivered to clients. Every detail has to adhere to the high standards set during the engineering process. From steel plates to software. Supply chain logistics, lead times, and environmental impact are all involved in the production plan. Whether it is a small backhoe or a 100-ton mining excavator, accuracy in production makes the work of a machine constant and durable.